Jungheinrich automates Coca-Cola HBC plant
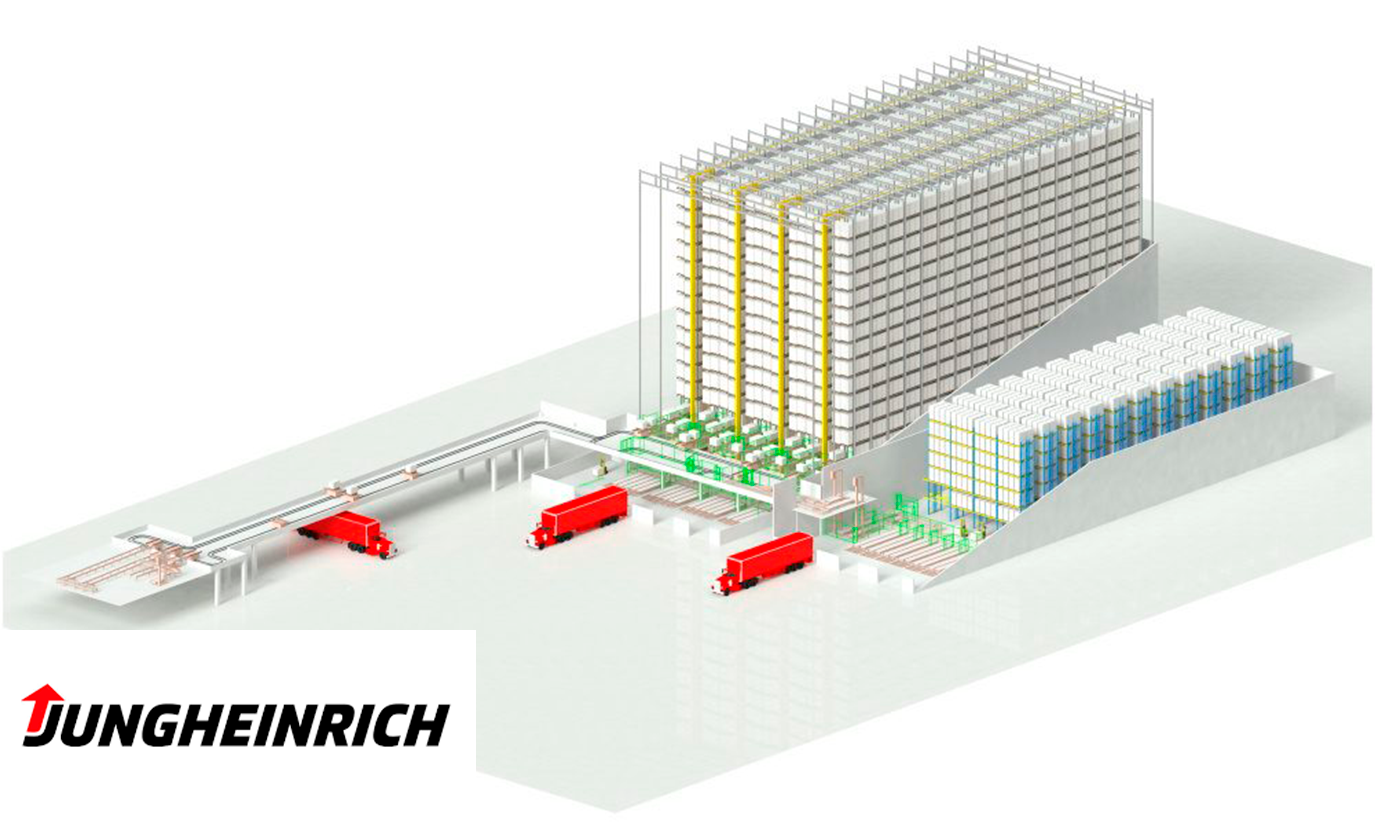
Jungheinrich is developing an automation solution for Coca-Cola HBC at its plant in Radzymin, Poland.
The new storage system aims to expand the existing facility and offers state-of-the-art technology. Some construction measures will be finalised during ongoing operations. Commissioning is scheduled for 2022. Making full use of the available space, creating more storage capacity and increasing throughput were the challenges that Coca-Cola HBC set Jungheinrich.
For the implementation, the intralogistics specialist opted for the construction of a 42-metre-high, 60-metre-long self-supporting vertical warehouse that ensures maximum space utilisation as well as high handling capacity. The automated vertical warehouse comprises a total of four aisles and offers space for up to 14,000 beverage pallets, which can be stored double-deep. All processes at warehouse height are fully automated. The Jungheinrich experts designed this warehouse with the option of expansion, making it possible to add aisles at a later stage without any complications.
The new Jungheinrich solution also improves the production transport route. To this end, changes were made as well as the expansion of existing conveyor systems: A monorail system with a bridge is now the heart of Radzymin. It transports ready-to-drink bottles to all available storage locations – both in the new vertical warehouse and in the automated warehouses.
Jungheinrich’s tailor-made intralogistics concept enables an optimised flow of materials between the different areas of the plant. Szymon Matulka, BU Engineering Manager Poland & Baltics at Coca-Cola HBC, said: “The installation is something special for us. With the automated warehouse and improved transport routes, we have set standards in terms of efficiency and safety. In this way, we guarantee a consistently high availability of our products. ” In addition, storage and retrieval machines from Jungheinrich subsidiary MIAS bring speed to the automated pallet warehouse. Thanks to special devices, high speed prevails during and when retrieving goods weighing up to seven tonnes.
Here too, additional devices can be integrated if required. In addition, the existing Warehouse Management System (WMS) was replaced. In future, Coca-Cola HBC will use only one WMS for the entire warehouse, which includes several intralogistics solutions. This will be used to manage all facilities and processes. The software helps to identify possible optimisations, such as the distribution of goods to the different locations in the warehouse. On this project, Lech Sowinski, Project Manager Technical Sales ASRS at Jungheinrich, explains that: “For Jungheinrich, cutting-edge intralogistics means efficient and cost-effective warehouse concepts. This is exactly what the solution we developed for Coca-Cola HBC in Poland offers. The new warehouse impresses with an optimised material flow. Since all operations come from a single source, fast integration and optimal communication between systems are also possible. “
Ricardo Costa will be the keynote speaker for EMPACK AND LOGISTICS & AUTOMATION PORTO
Ricardo Costa will be the keynote speaker for EMPACK AND LOGISTICS & AUTOMATION PORTO Pioneering in the creation of a Happiness Department in the company
More than 60 exhibitors and new products already confirmed for EMPACK AND LOGISTICS & AUTOMATION PORTO
More than 60 exhibitors and new products already confirmed for EMPACK AND LOGISTICS & AUTOMATION PORTO The fair brings together the latest innovations in packaging,
EMPACK AND LOGISTICS & AUTOMATION IS BACK IN PORTO ALREADY IN APRIL
EMPACK AND LOGISTICS & AUTOMATION IS BACK IN PORTO ALREADY IN APRIL The largest trade fair dedicated to professionals in the packaging, storage, maintenance, logistics,
“A coffee with…” LEYRE GUTIÉRREZ DURÁ- Specialist in Packaging and Neuromarketing
“A coffee with…” LEYRE GUTIÉRREZ DURÁ- Specialist in Packaging and Neuromarketing Empack and Logistics & Automation Porto: You have a long career in the packaging